Client
Selco Foundation
Work at 45°C - Workshops of Blacksmiths
Selco Foundation
It is proven that physical environment impacts quality of work, as seen in the case of Blacksmith industries in Dharwad. Given the climate of the region, and the nature of work which is heat intensive, there are long term effects on the physical health of the blacksmiths. The main factors that lead to loss of comfort and productivity are - heat and smoke due to the forge, noise generated from hammering and the use of power tools, and overall physical exertion.
Selco interventions include passive methods tailormade to suit the context and the needs of the craftsmen. The goal is to solve primary concerns of heat and ventilation for better working conditions and comfort for the people involved..
Category
Documentary Film
Work at 45°C - Workshops of Blacksmiths
Selco Foundation
It is proven that physical environment impacts quality of work, as seen in the case of Blacksmith industries in Dharwad. Given the climate of the region, and the nature of work which is heat intensive, there are long term effects on the physical health of the blacksmiths. The main factors that lead to loss of comfort and productivity are - heat and smoke due to the forge, noise generated from hammering and the use of power tools, and overall physical exertion.
Selco interventions include passive methods tailormade to suit the context and the needs of the craftsmen. The goal is to solve primary concerns of heat and ventilation for better working conditions and comfort for the people involved.
Born out of thick white fumes,
molded by thudding echoes,
cast in burning red hot iron soft,
and sharp taste of metal in air,
emerges the glistening tool.
In the heart of Dharwad's business district is a blacksmith cluster that is a hub of tool making. Their key markets are the agricultural (implements like shovels, machetes) and construction (scaffolding, centring) industries. Farmers from villages as far as 20-30 km away travel to this location to place orders, and wait until the tool is ready to be carried back. This clientele makes the kharif and rabi seasons vital to the blacksmiths. Hence the proximity of the blacksmith cluster to the City Bus Terminus (CBT) makes it accessible and well connected.
The Ghisadi Khambar are a community of people from Maharashtra that are traditionally into tool making and repairing. The profession has been vamsha paaramparik (passed down for generations), while being entrepreneurial even under the rule of monarchs. They did not prefer ghulaamgiri (employment), and have largely been masters of their own craft.
Fire that is kept burning all day in the forge is symbolic of the constant demand for the tool - a basic entity used in the production and management of food, shelter, defense, art and craft - since prehistoric times.
Blacksmithing involves usage of tools like
ikkala
(tongs),
suttige
(hammer),
chaana
(chisel), and the application of the mind along with physical strength. A job that takes two days to complete with physical effort can be done in two hours by employing the right technique. Additionally, much of the manual labor can be replaced by machines to significantly reduce the time and effort required.
Over the years, many of them migrated to different parts of and beyond the state in search of work. Around the year 1830, the British arrived in Dharwad and commenced the establishment of an urban corporation. The growing need for fabrication work offered employment opportunities to skilled entrepreneurs like blacksmiths from nearby areas.
One of the five workshops in this cluster belongs to Mr. Pawar, whose great grandfather was granted a large parcel of land on moving to Dharwad from Indi taluk, Bijapur (on horseback) during the early nineteenth century. Eventual distribution of the plot of land led to five individual units adjacent to each other, all run by members within the family.
While it takes an average of two hours to make about fifty medium sized tools, machines render the job in half an hour. However, manual work is inevitable in the making of smaller tools requiring finer detail which cannot be done using the machine.
Making of large tools generally takes a couple of hours per piece - one hour to heat the iron rods, and another to hammer, shape and sharpen the heated iron into a tool - a process which is made convenient by the machine hammer. Finishing is done once the shaped iron tool cools down. Maintenance involves the repair of belt, bearings, solar battery, oiling of machines, etc.
The occupational hazards of blacksmithing manifest as physical discomfort and stress on a daily basis, to occasional injuries and possible permanent damage of many kinds. Mr Pawar suffers from limited hearing due to the hammering machine. Breathing difficulties and body aches are common. Regular anti tetanus injections are taken to prevent septic from the exposure or wounds caused by fine iron pieces. The flame is covered by moistened rice husk to heat the iron faster and equally, and also reduce the smoke produced. Yet, the frequency of complaints from neighbors about high levels of smoke in the vicinity compelled the blacksmiths to construct chimneys for its diversion.
During summers, the general daily average of 20-25 customers may increase to even 50 per day, extending the 8.00 am to 10.00 pm work day indefinitely. The nature of work varies on a day to day basis, from the replication of common tools that are usually in demand, to fabrication of tools - big and small - made to order. During the first wave of the COVID-19 pandemic, it was business as usual for the blacksmiths due to the dependence of farmers on blacksmiths - and so their unit had shifted temporarily to continue functioning, along with support of the local police. Advancement in the blacksmith industry involves mechanization and usage of alternate energy sources to bring about ease and efficiency in the work intensity.
Mr. Pawar’s unit is mechanized incorporating a solar blower (reducing the need for rice husk by 80%) and a hammering machine (purchased on a loan of Rs. 2 lakh). The workshop now functions with 3 less workers, resulting in savings of Rs. 45,000 on salaries alone. After switching to solar energy, the electricity bill has been brought from Rs.1,000 to zero even with the welding and drilling machines. The savings contribute to future goals and aspirations such as children's education, weddings and other functions in the family. The unit is a successful model for blacksmiths in the region to learn from and pursue growth and development - both from the livelihood and family perspectives.
Produced by
Teepoi LLP
Commissioned by
Selco Foundation
Content, Direction
Karishma Rao
Cinematography
Vishwesh Shiva Prasad
Vinayak Bhat
Photography
Vandana Druva Kumar
Suchit Puri
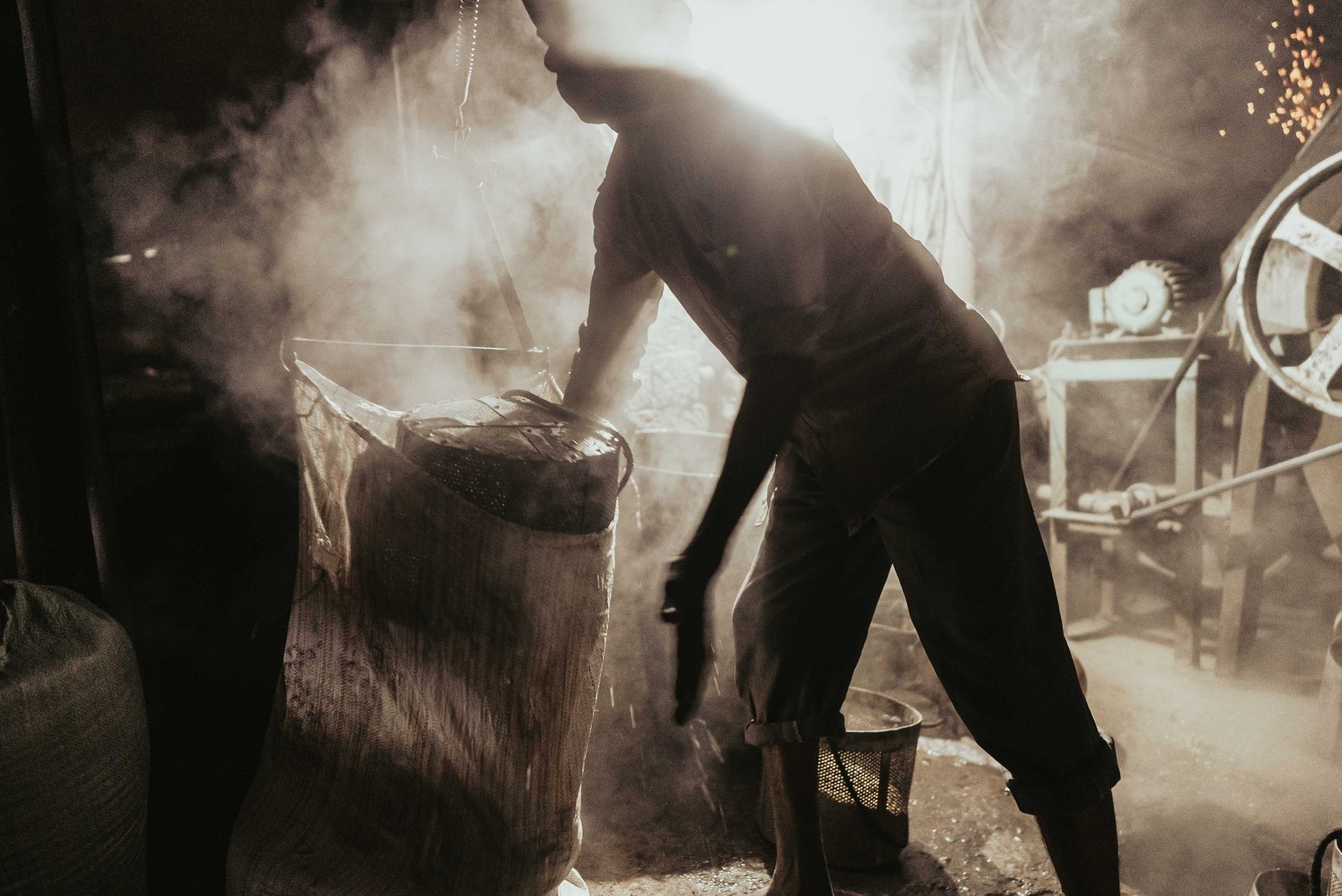
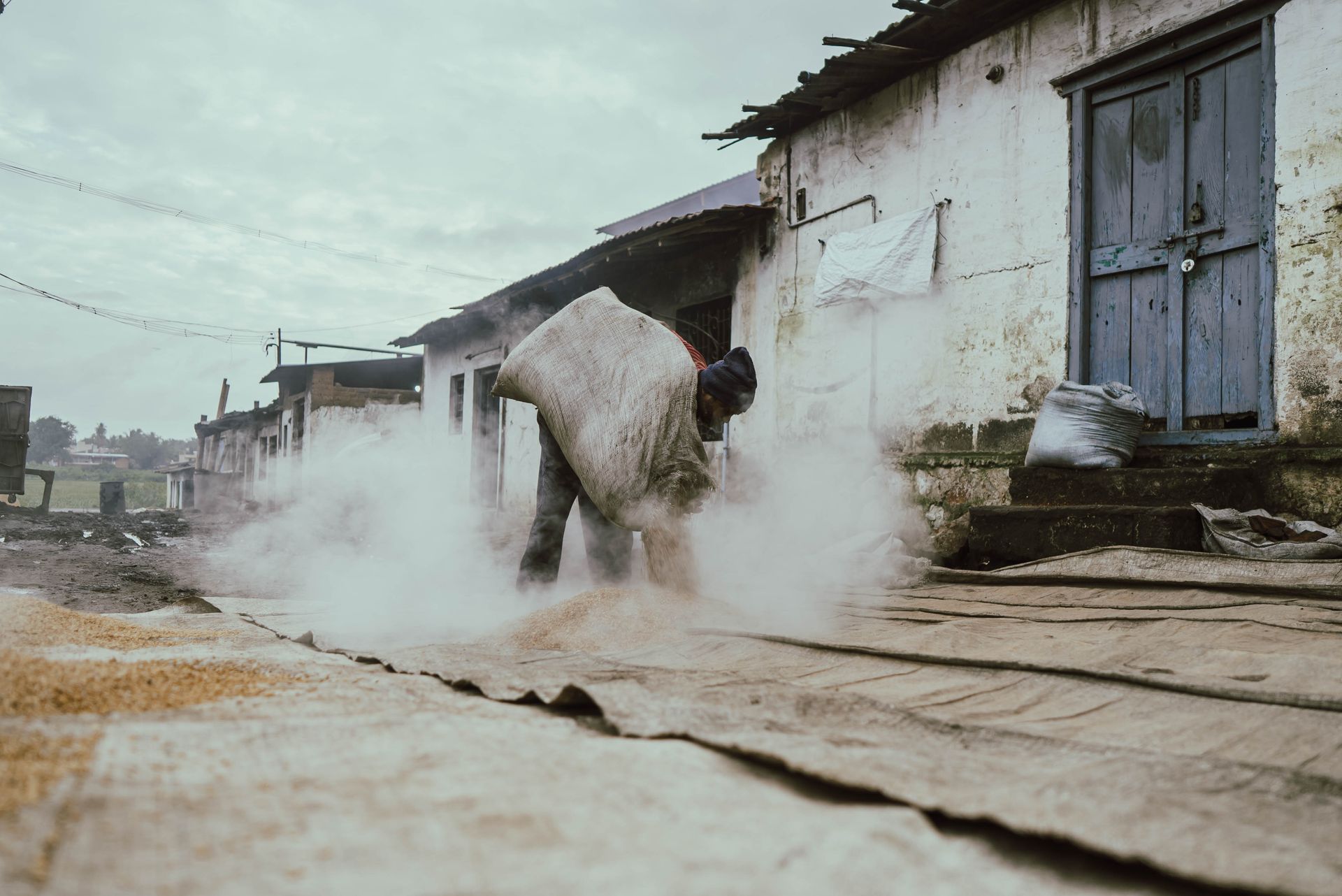
LA Journal
Selco Foundation's article as published in Landscape Architecture Journal Issue #70.
Born out of thick white fumes,
molded by thudding echoes,
cast in burning red hot iron soft,
and sharp taste of metal in air,
emerges the glistening tool.
In the heart of Dharwad's business district is a blacksmith cluster that is a hub of tool making. Their key markets are the agricultural (implements like shovels, machetes) and construction (scaffolding, centring) industries. Farmers from villages as far as 20-30 km away travel to this location to place orders, and wait until the tool is ready to be carried back. This clientele makes the kharif and rabi seasons vital to the blacksmiths. Hence the proximity of the blacksmith cluster to the City Bus Terminus (CBT) makes it accessible and well connected.
The Ghisadi Khambar are a community of people from Maharashtra that are traditionally into tool making and repairing. The profession has been vamsha paaramparik (passed down for generations), while being entrepreneurial even under the rule of monarchs. They did not prefer ghulaamgiri (employment), and have largely been masters of their own craft.
Fire that is kept burning all day in the forge is symbolic of the constant demand for the tool - a basic entity used in the production and management of food, shelter, defense, art and craft - since prehistoric times.
Blacksmithing involves usage of tools like
ikkala
(tongs),
suttige
(hammer),
chaana
(chisel), and the application of the mind along with physical strength. A job that takes two days to complete with physical effort can be done in two hours by employing the right technique. Additionally, much of the manual labor can be replaced by machines to significantly reduce the time and effort required.
Over the years, many of them migrated to different parts of and beyond the state in search of work. Around the year 1830, the British arrived in Dharwad and commenced the establishment of an urban corporation. The growing need for fabrication work offered employment opportunities to skilled entrepreneurs like blacksmiths from nearby areas.
One of the five workshops in this cluster belongs to Mr. Pawar, whose great grandfather was granted a large parcel of land on moving to Dharwad from Indi taluk, Bijapur (on horseback) during the early nineteenth century. Eventual distribution of the plot of land led to five individual units adjacent to each other, all run by members within the family.
While it takes an average of two hours to make about fifty medium sized tools, machines render the job in half an hour. However, manual work is inevitable in the making of smaller tools requiring finer detail which cannot be done using the machine.
Making of large tools generally takes a couple of hours per piece - one hour to heat the iron rods, and another to hammer, shape and sharpen the heated iron into a tool - a process which is made convenient by the machine hammer. Finishing is done once the shaped iron tool cools down. Maintenance involves the repair of belt, bearings, solar battery, oiling of machines, etc.
The occupational hazards of blacksmithing manifest as physical discomfort and stress on a daily basis, to occasional injuries and possible permanent damage of many kinds. Mr Pawar suffers from limited hearing due to the hammering machine. Breathing difficulties and body aches are common. Regular anti tetanus injections are taken to prevent septic from the exposure or wounds caused by fine iron pieces. The flame is covered by moistened rice husk to heat the iron faster and equally, and also reduce the smoke produced. Yet, the frequency of complaints from neighbors about high levels of smoke in the vicinity compelled the blacksmiths to construct chimneys for its diversion.
During summers, the general daily average of 20-25 customers may increase to even 50 per day, extending the 8.00 am to 10.00 pm work day indefinitely. The nature of work varies on a day to day basis, from the replication of common tools that are usually in demand, to fabrication of tools - big and small - made to order. During the first wave of the COVID-19 pandemic, it was business as usual for the blacksmiths due to the dependence of farmers on blacksmiths - and so their unit had shifted temporarily to continue functioning, along with support of the local police. Advancement in the blacksmith industry involves mechanization and usage of alternate energy sources to bring about ease and efficiency in the work intensity.
Mr. Pawar’s unit is mechanized incorporating a solar blower (reducing the need for rice husk by 80%) and a hammering machine (purchased on a loan of Rs. 2 lakh). The workshop now functions with 3 less workers, resulting in savings of Rs. 45,000 on salaries alone. After switching to solar energy, the electricity bill has been brought from Rs.1,000 to zero even with the welding and drilling machines. The savings contribute to future goals and aspirations such as children's education, weddings and other functions in the family. The unit is a successful model for blacksmiths in the region to learn from and pursue growth and development - both from the livelihood and family perspectives.
credits
Produced by
Teepoi LLP
Commissioned by
Selco Foundation
Content, Direction
Karishma Rao
Cinematography
Vishwesh Shiva Prasad
Vinayak Bhat
Photography
Vandana Druva Kumar
Suchit Puri
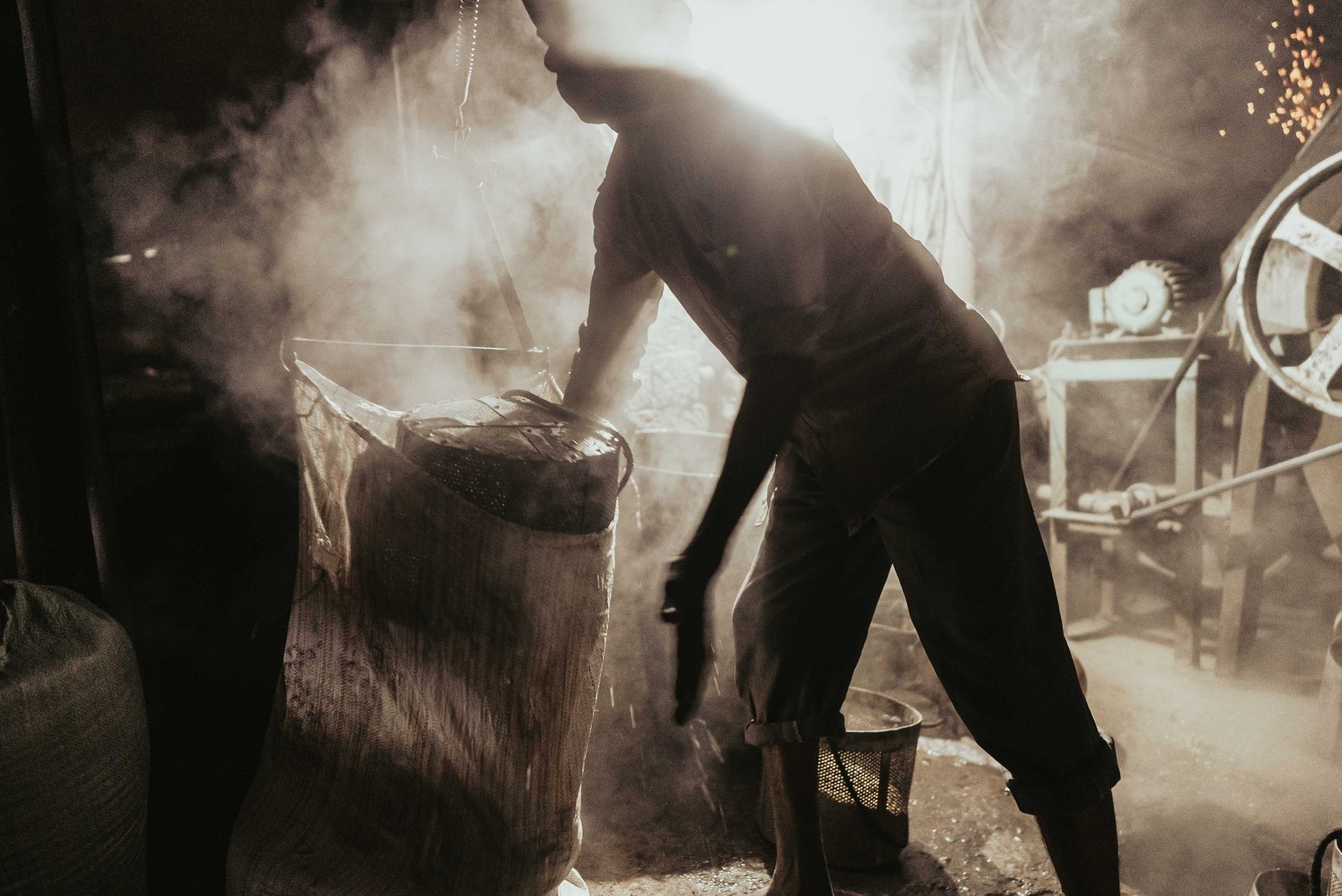
LA Journal
Selco Foundation's article as published in Landscape Architecture Journal Issue #70.